The role of asset tracking software in the construction industry
The construction industry is a burgeoning sector, hammering out the very foundations of modern society as we know it. According to the Bureau of Labor Statistics, the number of people working in this sector was close to ten million as far back as 2014. However, construction projects aren’t just about managing surveyors, builders, and foremen; there is also a staggering amount of equipment to procure, distribute, and maintain on the regular.
The construction equipment market is projected to amount to 192 billion USD in 2017!
While solutions like construction management software can aid companies in organizing and streamlining the human elements of construction, there is also a dire need to track and manage construction equipment. In fact, a lot of the challenges associated with the construction industry seem to revolve around the use and management of assets. In other cases, efficient asset lifecycle management can also alleviate problems in seemingly unrelated operational spheres. This post will take you through some of the major challenges faced by the construction industry, and demonstrate how your company can use asset tracking software to overcome them.
Resource management before anything else
Construction management often becomes a game of resource management. A huge part of this is managing construction assets. In fact, this could be an ever bigger deal in the future, as reports suggest that drones and other equipment could save companies a whopping 127.3 billion USD in labor! For now, companies must ensure all their crew members have tools in hand, that their materials inventory is well-stocked, and that cranes and diggers aren’t overbooked when they’re needed. Equipment tracking software can take out a lot of the guesswork involved in such processes, ensuring that all equipment is logged and accounted for. You can track individual pieces of heavy machinery using barcodes and QR codes, and set low stock alerts on construction consumables, so you’re never out of the little bits and bobs that somehow manage to run your projects over schedule. Every little step you can take to mitigate industry obstacles can be a huge help. Imagine a system that allows you to know when certain machinery is booked, create purchase orders online instantaneously, and manage vendor details on the cloud! This can ensure that you’re never wasting human or monetary resources while you wait on certain tools to get the job done.

Fight function creep to stay on target
Function creep refers to the gradual growth in the scope of a project. The construction industry is particularly vulnerable to this, as projected tasks slowly get more complicated, unplanned duties keep popping up, and inefficient scheduling requires workers to take the long route out of problems. This not only leads to bloated budgets and time overruns, but can also amplify costs related to gathering materials, machinery, and crew members on short order. This is especially important considering that 70% of all construction projects experience a time overrun. Clamoring to get people and equipment to work overtime or out of schedule is therefore a huge hassle. Asset tracking software allows you to fight function creep through in-depth data management and actionable insights. You can peruse reports on asset utilization and maintenance, and also keep track of work orders so you can stay on top of tasks throughout the course of a project. This type of close monitoring helps you stay on target and consistently battle rising costs!
Compliance is the new ‘License to Operate’
The need to be compliant with industry guidelines is becoming increasingly more important for companies worldwide. This is especially true for the construction sector, with administrative bodies like OSHA really revving up the importance of meeting health and safety standards. In fact, in 2006, more than 59% of all OSHA inspections conducted in America took place within the construction sector. This is why an asset tracking software that helps you meet compliance guidelines can be a really good investment. Not only does it help you keep tabs on huge swathes of equipment using dynamic custom fields and historical data, but you can also pay specific attention to the maintenance of your construction assets. This would allow you to prioritize certain items for maintenance over others, organize recurring servicing tasks, and carry out preventive maintenance by managing custom alerts. This is really crucial because poorly maintained equipment can increase the instances of injuries on construction sites. Seeing as the construction industry has the second highest fatality rate in all of America, construction companies need to make sure they’re taking the extra step when it comes to compliance requirements.
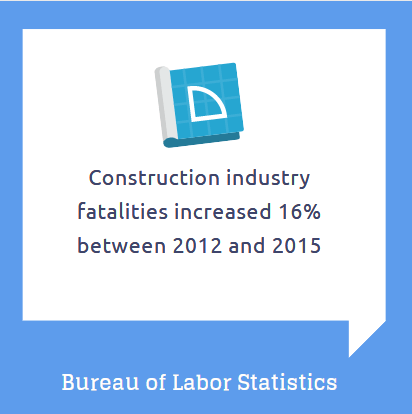
Build an accountable workforce
Encouraging transparency in your organization is extremely important if you are to meet your goals on time and on budget. Asset tracking software can help employees be a lot more accountable. This can be done in many ways. For example, you could keep histories of machine custodianship so you know exactly when damage occurred to a specific item. You could also draw up employee reports to see how they’ve been managing and engaging with work orders and other procurement or retirement tasks. This kind of remote supervision is a great tool for construction managers, because it gives them all the benefits of close monitoring without any of the effort.
Additional reading: Find out how an ATS works
This is especially crucial for the construction sector, as 92% of the individuals working in this industry have experienced theft in one form or another! However, it isn’t just theft that construction companies – with huge amounts of equipment at their helm – need to worry about. Bolstering accountability can also lower instances of misplaced, mismanaged, or lost items.
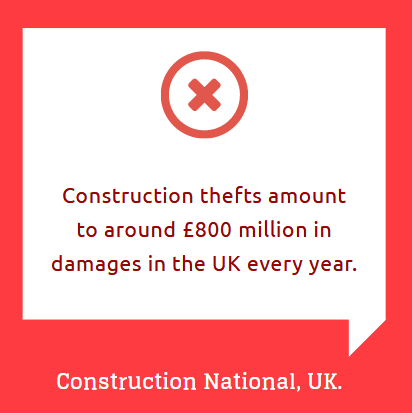
Communication is still king
Employees who don’t feel invested in your company’s goals are far less likely to feel motivated to do a good job. This is why engaging employees is vital for the smooth functioning of business processes. Coordination and communication not only helps employees be more devoted to your company ideals, but it also streamlines workflows and makes things a lot more efficient. This is where a cloud based asset tracking solution would be very useful. Different departments can liaise with each other, share details about their reservation schedules, and co-manage data to improve the flow of information across different organizational levels. Collaboration in this way reduces redundancies, allows for the creation of important informational linkages, and helps everyone feel like they are serving a bigger purpose! Not surprisingly, research has suggested that collaborative tools are a brilliant way to improve efficiency in construction management.
Conclusion
The construction industry is still open to improvement. Its two main concerns, boiled down to their very core, seem to be the management of people and assets. Asset tracking software can help with the latter, allowing companies to not only improve workflows and streamline business operations, but also lower costs and stick to tight schedules through more efficient asset and inventory management. So if you’re looking for solutions to these major construction industry challenges, look no further than a great asset management platform!
This article was contributed by leading asset tracking software EZOfficeInventory. Featured on TechCrunch, it is enabling thousands of construction businesses to lower costs, improve workforce accountability, and streamline workflows. Click here for more details on asset tracking software for construction industries.