When it comes to delivering successful builds, quality assurance and quality control in construction are essential. Clients insist on results that not only fulfill the design specifications but also the highest achievable industry standards. But how do you deliver high-quality results on-site? The answer is to develop a clear, concrete plan that involves both quality assurance and quality control from start to finish.
In this article, we’ll explore how to safeguard the quality of your work and why mastering quality assurance and quality control in construction is the foundation of consistent project success.
What is quality assurance and quality control in construction?
To begin, it’s important to understand the distinction between the two terms:
- Quality assurance (QA) is all about processes and systems. It’s proactive—designed to prevent defects before work even begins.
- Quality control (QC), on the other hand, is reactive. It involves inspecting and testing the actual work to detect and correct errors before they affect the completed work.
Together, quality assurance and quality control in construction provide a comprehensive system for delivering high-quality results on every construction site.
👉 Learn how LetsBuild helps manage quality on site with real-time updates and digital inspections
How to ensure quality assurance and quality control in construction
Now that we’ve defined the terms, let’s look at how to apply QA/QC to your projects.
1. Set clear quality objectives
Start every project with well-defined, quantifiable quality goals. A good plan outlines the requirements to attain, how they can be measured, and who will track them. Clarity is the basis of successful QA/QC implementation.
2. Develop a solid QA/QC plan
A comprehensive plan is the backbone of quality assurance and quality control in construction. It should include:
- Inspection and testing procedures
- Acceptance criteria
- Reporting structures
- Corrective action protocols
When your team knows the expectations, it’s easier to keep everyone aligned.
📄 Free eBook: Unveil the path to digital transformation in construction
3. Work with trusted suppliers
Even the best crew can’t deliver quality using poor quality materials. Part of QA/QC involves locating good vendors, verifying certifications, and checking that materials meet specifications before use.
4. Train your team
People are the heart of any QA/QC initiative. Regular training ensures that everyone, from site foremen to subcontractors, understands what’s needed and how to meet those standards.
5. Conduct routine inspections
Scheduled inspections help catch problems early, reduce rework, and ensure each phase meets the required standards. This is a core part of delivering high-quality results consistently.
6. Document everything
Documentation is critical in QA/QC. From material records to daily site reports, a clear paper trail keeps you compliant and protects you from disputes.
More to read: The best methods to site construction quality control
7. Prioritise communication
Consistent updates across teams help keep quality on track. Whether it’s reporting an issue or confirming a fix, strong communication ensures no detail falls through the cracks.
8. Use the right technology
Digital solutions make QA/QC much more achievable. Real-time reporting, mobile checklists, and centralised documentation help you stay on top of quality, even in fast-paced projects.
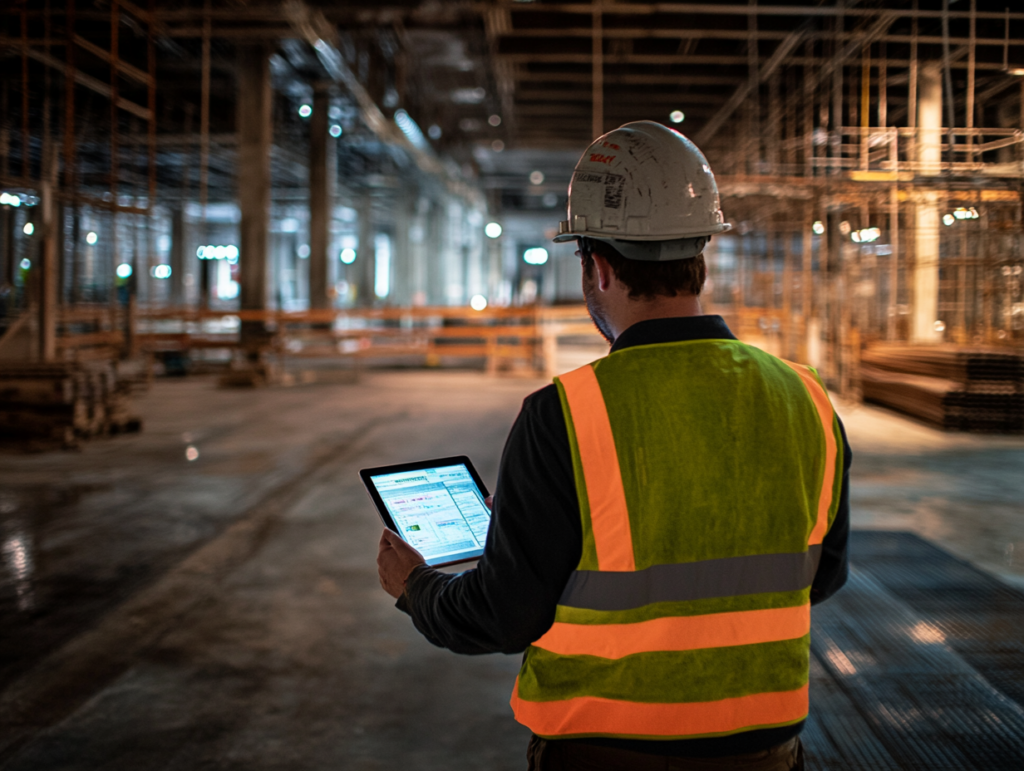
Common challenges in QA/QC for construction projects
Despite best efforts, construction teams often face hurdles when managing QA/QC:
- Tight deadlines limiting thorough inspections
- Poor documentation habits
- High staff turnover
- Misalignment between stakeholders
Identifying these risks early allows you to put systems in place that minimise their impact and keep your QA/QC efforts effective.
Further reading: Common mistakes in construction quality assurance and how to prevent them
Final thoughts
So, how do you ensure quality control on a building project? It’s about planning, precision, and ongoing communication. A strong focus on QA/QC helps you meet—and exceed—expectations every time.
By building quality into your processes, training your team, inspecting diligently, and using the right tools, you create a foundation for excellence in every project.
In the end, quality assurance and quality control in construction is more than a checklist—it’s a mindset that drives every successful build.
How LB Aproplan supports quality assurance and quality control in construction
If you’re looking to take your QA/QC to the next level, LB Aproplan by LetsBuild is the tool you need.
LB Aproplan is purpose-built for site teams who want to streamline inspections, improve communication, and ensure compliance—all from a single platform. With it, you can:
- Create and assign digital checklists for consistent site inspections
- Instantly report and track defects with photos, comments, and deadlines
- Keep all quality documentation in one secure, searchable place
- Collaborate in real time across teams and subcontractors
- Monitor progress and corrective actions from your mobile device
By digitising your QA/QC processes, LB Aproplan helps you reduce costly errors, speed up site follow-up, and deliver projects that meet the highest standards.