Us muddy-boot brigade, like, we know of one major risk on a construction site that is never mentioned by academics or those writing articles on the subject. That is we look for “The bloke who is an accident looking for somewhere to happen” – and we get rid of him
When inducting new arrivals on site I have always stressed that I want them to look for “the bloke that is the accident looking for somewhere to happen” and to let me know pretty darned quick. They always agree enthusiastically and wholeheartedly with this request because they know full well that the accident that happens might not be to that man but to some other person or persons.
With this approach to risk on site I take great pride in the fact that in 40 years as a manager on construction sites I have only ever had two Notifiable Accidents. Both these incidents occurred when the men were working out of sight of anyone else. Neither incident was prosecuted by HSE and both guys got fired for being idiots! Thankfully, neither put anyone else at risk.
Oh! I can think of one other very silly risk on a site of mine. This one didn’t put people or the job at risk but did cost the guy money. We were doing concrete repairs to the support beams of a raised motorway and using high-pressure water jets to cut the defective concrete. This gentleman thought it would be a very good idea to use this plant to clean his car. It got is bonnet very; clean stripped the plait off down to bare metal. Lol. He gave up at that point!
So okay, let’s have a look at the more serious, general risks that generally have to be taken into account on construction sites and how we stay ahead of them.
The High Cost of Lives Through Construction Defects
Over the years there have been some construction defects which have costs many lives. The first one I shall list wasn’t that dramatic. I’ll explain why I have included it later.
Supermarket in Riga, Latvia, 2009
In 2009 the flat roof over part of a supermarket collapsed. This collapse was caused by the weight of snow on the roof that winter. The collapse killed nine people and seriously injured another 17. It is just very lucky that this did not happen during a busy part of the day when they would have been far more people in the store.
The reason for this collapse was later found to be due to two Causes. The first was that the concrete itself was not up to the required standard of compressive strength. The second was that the calculations in designing the roof under-estimated the depth of snowfall. This is a little ironic because, in previous winters, there had been deeper snow. Presumably the roof concrete had been weakened in the previous years.
Now as to why I should put this at the top of the list. It was because, only weeks before, that my wife and I had been shopping in that supermarket under that very roof.
Lotus Riverside Complex, Shanghai
In that same year of 2009 there was a 13 storey apartment block nearing completion. As an afterthought excavations were undertaken to construct a garage space under the building. That in itself did not cause a problem. The removed Earth from the excavations, however, were dumped in a landfill next to a nearby stream.
The weight of all this earth caused the riverbank to collapse allowing water to seep into the ground causing a muddy foundation for the building. It was this that caused the building collapse. Fortunately only one worker on the site was killed by it.
This accident was caused by a risk which the professionals involved had simply not considered. It is not known whether the main contractor actually had enough knowledge to judge the risk is an acceptable or if they simply chose to ignore it.
Katowice International Fair Trade Hall, Poland
It was heavy snow in January 2006 which caused this building’s roof to collapse. It smashed down on the exhibition floor and trapped hundreds of people. These people were exposed to dangerous sub-zero temperatures. The lacerated metal acted like a freezer and rescuers were unable to heat air under the roof because parts of the collapsed roof were supported by nothing more than heaps of piled snow stop. While the rescuers were working a second section of the roof collapsed.
The collapse of this roof caused the death of 65 people and injuries to another 170.
It was found that this roof had buckled under snow for years previously and had been rebuilt. The rebuild, however, had been done without proper testing and inspections.
Hyatt Regency Walkway Collapse, Kansas City.
This disaster occurred in 1981. The hotel had suspended walkways four floors above a lobby. At the time there was a dance competition being held in the lobby. The collapse of the walkways killed 114 people and injured another 200.
Investigations showed that there had been design changes at a late date and these altered the methods in which the tie rods supporting the walkways were connected to them. This inadvertently caused the tie rods and support beams to carry the weight of both the fourth floor and second floor walkways. When the walkway collapsed the tipping point came because of the weight of people stood on it watching the dance competition. The tie rods and support beams were unable to handle this additional loading.
That this avoidable risk in construction was not avoided stresses the importance of good communication between design engineers, architects and contractors. It also highlights the importance of rigorous checks on design, especially any proposed by contractors.
Willow Island Cooling Tower, West Virginia
this disaster occurred in 1978 and killed 51 of the construction workers on site when the cooling tower collapsed.
Apparently the project been seriously behind programme and the workers on the site found ways to speed things up. These included fixing high-rise scaffolding to concrete which wouldn’t properly cured, using one of the wrong kind of bolts to fix the scaffolding together, and incorrectly installing a concrete hoisting system in a way which had not been subjected to a thorough engineering review.
This is believed to be the biggest construction site accident in US history.
Québec Bridge, Canada
This was a cantilever bridge being built to stretch across the St Lawrence River in 1907. An engineer working on the job reported by telegraph – (remember this was in the days before mobile phones) – that he had noticed the frame was starting to bend. This report was to the designer who was not working on the site.
At first, the designer completely ignored the engineers report and concern. He later to wire to the company building the bridge instructing them to put no more loading on the bridge until all the facts were considered. The chief engineer, however, ignored that instruction and work on the bridge continued. Not long afterwards the 150 feet tall bridge collapsed killing 75 workers.
An investigation after this accident revealed that the bridge weighed 4000 tonnes more than had initially been calculated and the beams were unable to handle this excess weight.
This is Canada’s worst bridge disaster and is a very sad reflection of both the designers, consultants and senior site management.
* * * * * *
So what we notice about all these did above disasters is that they were caused by der-brained plonkers, greedy so-and-so’s, sheer incompetence or by people not paying attention to what they were supposed to be doing.
The really sad part is that all these lives and all our money could have been saved if there had been an effective system of quality control in operation.
Quality Control – “De-Snag As You Go!”
To demonstrate the time and money that can be saved by this “de-snag as you go” I usually give a very simple example. We are building a house and one of the window frames is fitted out of vertical. If we notice this at the time and pointed out to the guys all they have to do is take out two screws, align the window frame and put two more screws in. That must take them all of five minutes.
If, however, this is noticed at the time what happens then? Well, on the inside the walls and the window returns get plastered, a sealant is laid around the window and the walls coat of emulsion put on them. Externally mastic is placed around the window frame and then the external walls are rendered and pebble dashed. How long does that take? Days? Weeks? – And how much does it cost whoever got it wrong the first place? Certainly enough money to seriously dent their profit margin.
Next let’s have a look at what is required from people to make sure that the de-snagging is done “as you go”. This is pretty simple and makes life pleasant for those who have the primary responsibility for this; the Site Management. All it requires is – and I have a published paper on this – to “Swan around site in a suit and tie and look important”! If we do this it means that any defects in workmanship are picked up immediately and it even has another couple of beneficial side-effects.
The first of these is the skilled tradesmen know that their work is going to be is closely inspected while they are still working on a particular Task, so, once that idea is in their heads they make sure they “get it right first time every time”. The second one is that, because the Site Manager, or whoever, is wandering around and looking, he will also be chatting to the skilled tradesmen. And you know what that chatting does? It helps us to make friends!
As an incidental aside there is another time-saving benefit associated with the suggested dress code. If someone arrives on site and asked who the gaffer is makes it quick and easy for the guys to just point and say “Him over there in the suit and tie”.
Okay, so we now all understand how this “de-snag as you go” saves time and money. The other thing that it saves is great heaps of paperwork! If there are no Notifiable defects to be corrected there is no need for any documentation to be sent to all and sundry to bring it to their attention and get it made good stop.
The other beneficial side-effect it has works on those who are not site-based but like to walk onto site, walk round poking their noses in and then make themselves feel important by producing this documentation. They soon get the idea and then make their site visits a social outing and an opportunity to bring themselves up to date with how the project is progressing. There is another beneficial side-effect, too. Because it makes these people confident the work is progressing as it should, they are subtly drawn in to feel they are part of the project Team. This makes them far more co-operative and, if information or input is requested from them, they tend to get it back to site far more quickly.
All of this leads on to the question of how do we get this “de-snag as you go” as an integral part of Quality Control? Well, there was an old-fashioned way that used to be implemented by “old guffers” like myself just like to wander round site and socialise. That achieved it without any fuss or bother but the downside was that it didn’t make the off-site personnel feel involved and automatically get quick responses from them when requested. We used to do this in the pre-digital and IT days.
So, flippancy aside, what actually has to be looked at? Well the whole thing, actually, from the time the building project is being designed. Building inspectors et alles have to look at the drawings and assess them for compliance with local and national codes, visual amenities locally and contract specifications. Once work begins on site commercial construction inspectors of got to inspect everything from foundations, framing, mechanical and electrical systems, roofing, drainage and everything else involved in the build. Come to think of it inspection responsibilities begin even before work starts on site. Things to be considered include soil conditions and the client’s requirements. Another one is the weather; for example a timber framed building can, under EuroCode 5, the up to 7 stories high. In the UK, however, because of our wind speed they can only go to 5 stories high. In the UK we just call the winds that cause this reduction in height a “windy day”. In other parts of the world such as California and the American Atlantic coast they call these winds “Hurricanes”. We British are so modest!
Okay so let’s get back to being sensible. To make sure that all these sensible judgements are made, along with, hopefully, daily site inspections of everything going on, what do we need from our Quality Control system to make sure that it happens?
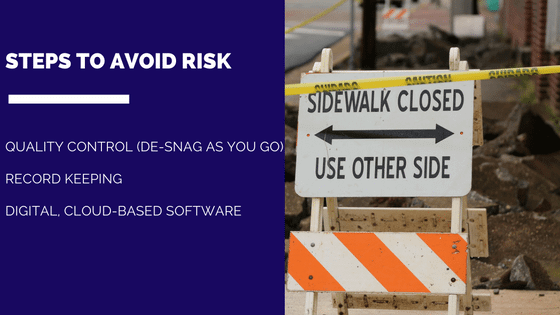
Record Keeping
That’s what we need; record-keeping!
I’m not proposing to go into this too deeply simply because we all know pretty well what documentation is required on a construction project. There is just one that I will point out because it is one that is required to be compiled by the site management, perhaps by every single person involved in the management of the construction site. That is a Site Diary in which is recorded every event which may affect the handover of the project to the Client. Some sneaky people, me for example, actually kept to site diaries. One of them was the property of the contractor for whom I was working; the second one was a personal, private diary in which I recorded questionable things which may, in the future, have come back to haunt me. Yes, on occasions this second diary has actually done that.
I used to keep them securely for several years and, five years after we had finished a job, I had a phone call from an insurance company. They had received a belated claim for injury incurred on the site. The sneaky little entry in my private diary reveal that he had actually received the injury off-site so he didn’t get any insurance money. Shortly afterwards I had a phone call from the Police about this incident. After reading out my diary entry to them and having my brain picked, the Police arrested this guy and charged him for the criminal damage he had done in the process of injuring himself. Probably worth adding that after his injuries the guy never did reappear on our site.
Another thing we all know is how much space all the paperwork to keep all these records occupies. In a site office the place is full of filing cabinets, shelves full of ring binders, cabinets for superseded drawings to go in and a drawing stand for current drawings. It can also occupy spaces on horizontal surfaces by being stacked up. The reason for this “stacking up” is usually because someone lacks the time or inclination to get it all filed away properly. Now that is just on site. In the contractor’s main office there is a similar amount of space occupied by the paperwork for the current project. However, the main contractor is required to keep all this documentation for six years. That means that they also have to pay for an archive to keep it all in. This same demand is also made on any of the professionals involved in the project such as architects, consultants and engineers. The construction client is also stuck with it for years and has to find somewhere to keep it.
All this time and space consuming paperwork is required, in the first instance, as an essential part of Quality Control. Wouldn’t it be nice if we could do away with it all? Agreed? So let’s have a look at how we can achieve that.
Digital, Cloud-Based Software
The solution to all this paperwork hassle has slipped in on us almost unnoticed. Like it or not we live in a digital age. Incidentally, there is a TV advert running in the UK the moment, which I hate simply because it’s true. It shows a bunch of seven-year-old kids boasting that they are better with IT than are we adults. Sadly, that is the truth of it. I hate to see my young grandchildren with their little fingers darting all over the touchscreen almost faster than my eyes can follow.
Anyway, these days it would be strange to find a fumble-fingered construction worker, from Project Manager through to Labourer, who didn’t have constantly to hand a “gadget”. That may be a PC, a tablet or a smart phone. Any of these will do the trick. Needless to say the clients, architects, consultants and everyone else involved as equal access to “gadgets”. That means that all we need to get rid of all the paperwork that a construction project generates is an App on all these “gadgets” to replace it.
If we have that means that everyone involved in the project from client down to site labourer can instantly know everything that is going on. How much time can this save? Well let’s say that something has to go in the post and then be copied and disseminated to everyone on site that needs to know. That alone can take up about a week. For the time and money that that alone can save if there is a drawing specification change just think of the example of house window that I gave earlier.
This App, assuming we have one, will also save all the time and money involved in handling and storing paperwork. It would also have another more subtle time and money saving effect.
An example of this would be if a Request for Information (RFI) was sent out. Everyone involved in the project would know that it had been which would place considerable pressure on the recipient the RFI. Concerns for their professional reputation and reliability would make sure that the information requested was sent out “pretty damned quick” (PDQ)! This PDQ would probably be well inside the usual seven days allowed by the contract for a reply. Just imagine how this could accelerate a project and slash time and money spent on rework. Even before work started on site the professionals and consultants involved in the design would check and double-check every single detail so they were shown up to be plonkers once work on site started.
This wonderful, indeed perfect, App that we would like would have on it absolutely all details of a project. This would start with Specifications and Bills of Quantity, drawings, revised drawings, photographs of the work, a build programme, memos and letters – indeed every single piece of paperwork relating to that project. The only exception to that would be any commercially confidential communication.
As for keeping records of this project for the statutory six years, that too would be a problem resolved. That would be down to the provider of this wonderful, wonderful App. Just as they keep all current records in the Cloud they would also keep the historical records of completed projects in the Cloud.
Sewers were coming to the end let’s have a look at how this App would improve Quality Control beyond all recognition. That comes down the daily walkabout looking for defects in workmanship. Now the public perception is that all construction workers are a bunch of “der-brains” and that includes management. However the reality is that skilled tradesmen do have an awful lot of professional pride. Using this App they know that any defects would be marked against that Task on the Build Programme. They know that everyone would know that they had been “naughty boys” so their professional pride would make sure that they got it “right first time every time”!
Well, for you folks who haven’t already worked it out for yourselves, this App does exist. It is called GenieBelt. What a time and money saver it is! Time and money are saved on not having to handle and store paperwork, plus it can also have the unexpected benefit of actually accelerating the project and getting the site handed over ahead of time.
So to save all that time and money how much will GenieBelt cost? Based on sums I did some time ago the cost of handling and storing the paperwork for a £5 million project that ran for six months would be about £68,000. GenieBelt, for a similar project, would cost about £10 per month; a total of £60. So how does a saving of £67,940 sound to you?
Not only that – It has “Kept You ahead of Risk”!
* * * * *
Case pretty well proven! Use that wonderful GenieBelt App and you will see phenomenal improvements in the accuracy accessibility and accountability of your construction project. You will also see large time and cost savings.
Come on everyone! We live in today’s digital world, so kick out your paperwork and:-
– go GenieBelt !!!